Yli 100 vuoden sitoutuminen tekniseen kehitykseen on tehnyt meistä johtavan valmistajan muuttuvien AC-taajuusmuuttajien, servokäyttöjen, ohjaustekniikan ja robotiikan aloilla.
Getting started with the HC online tutorial!
This e-learning introduces the HC10 with a YRC1000micro controller and the Smart Pendant!
Cobot Portfolio
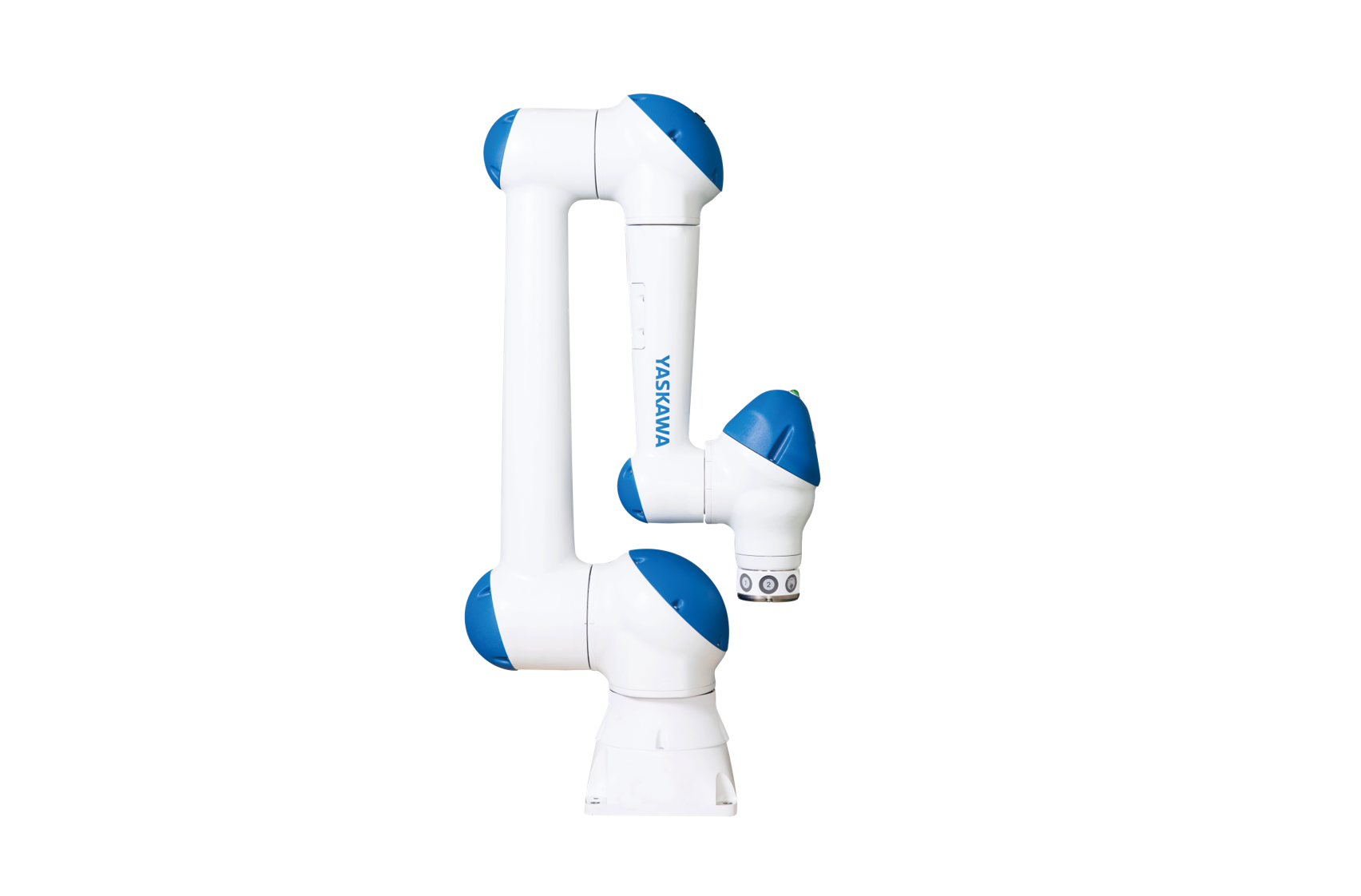
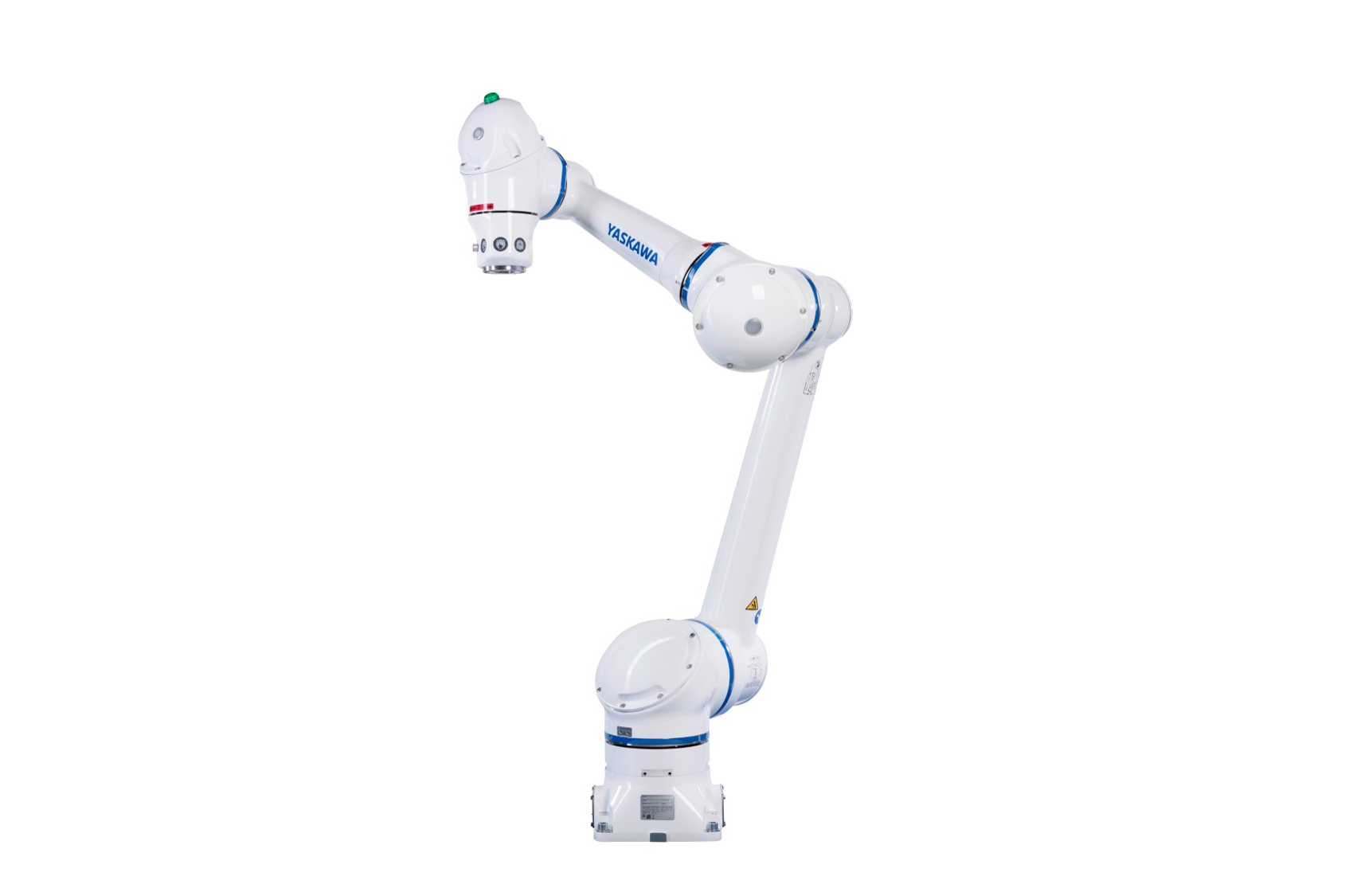
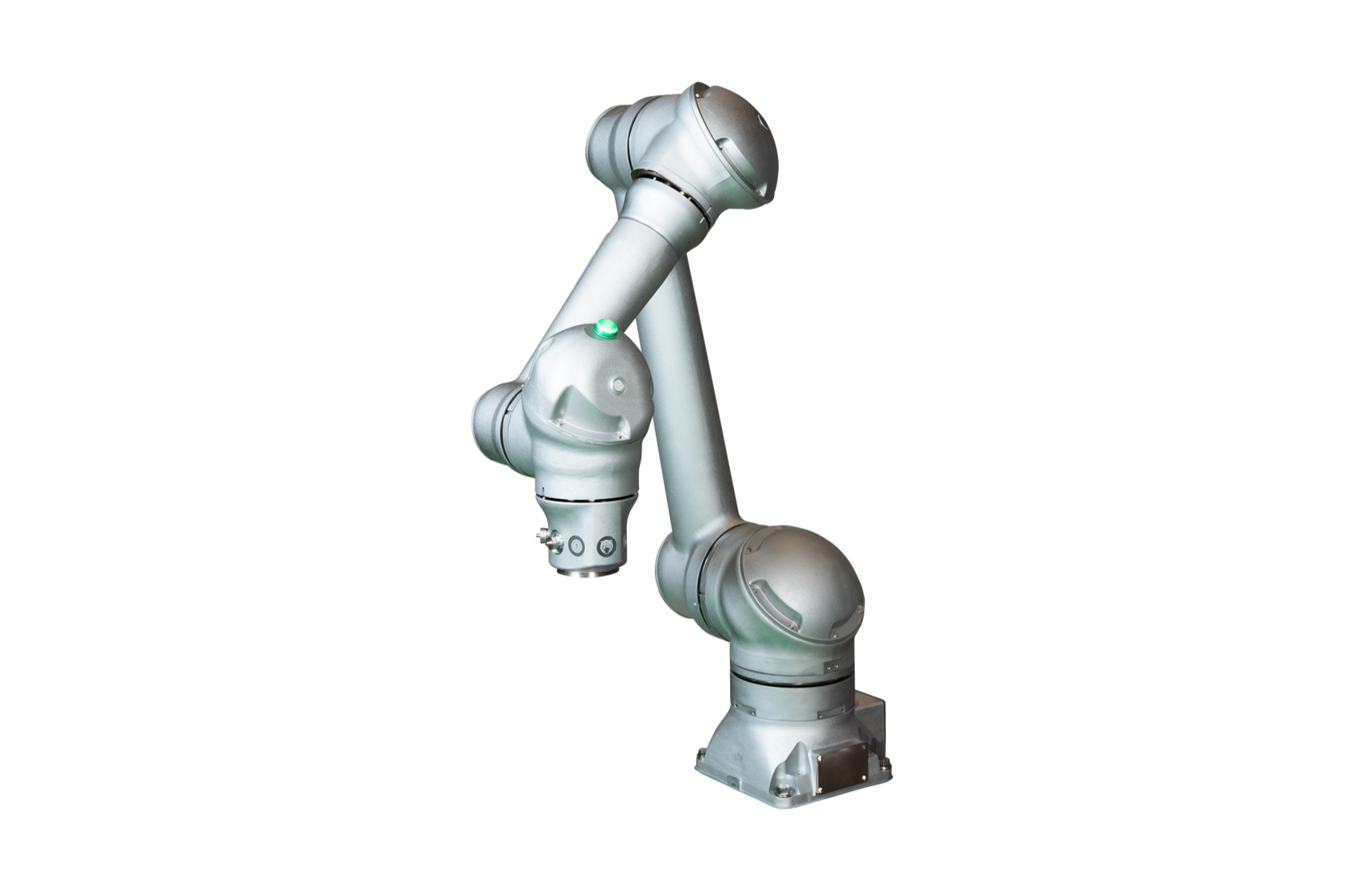
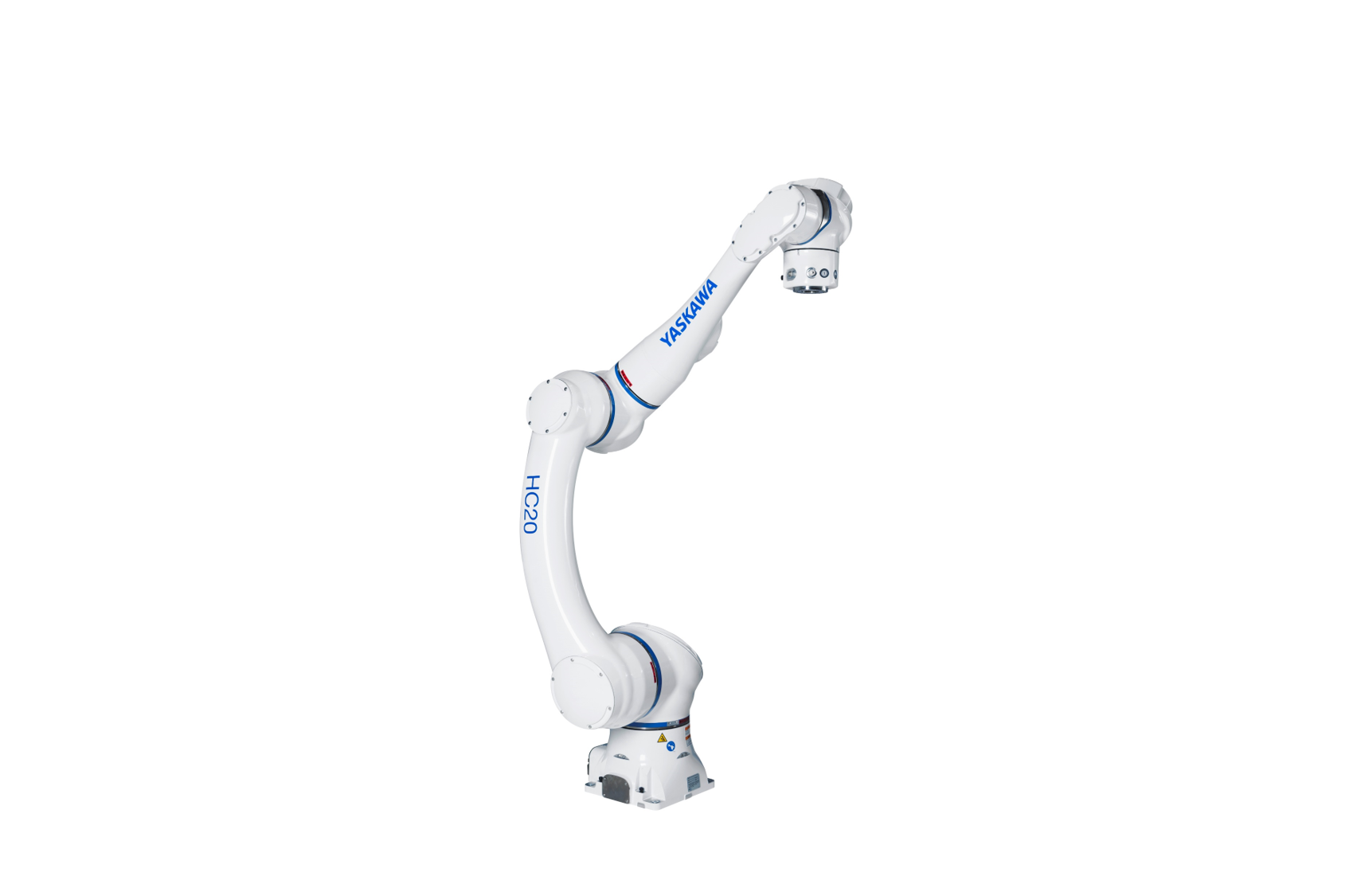
HC10DTP Classic
HC10DTP
HC10DTFP
HC20DTP
1) Plug&Play ISO Flange
2) Direct Teach Hub
3) Status LED & Resume Button
4) Servo-On LED
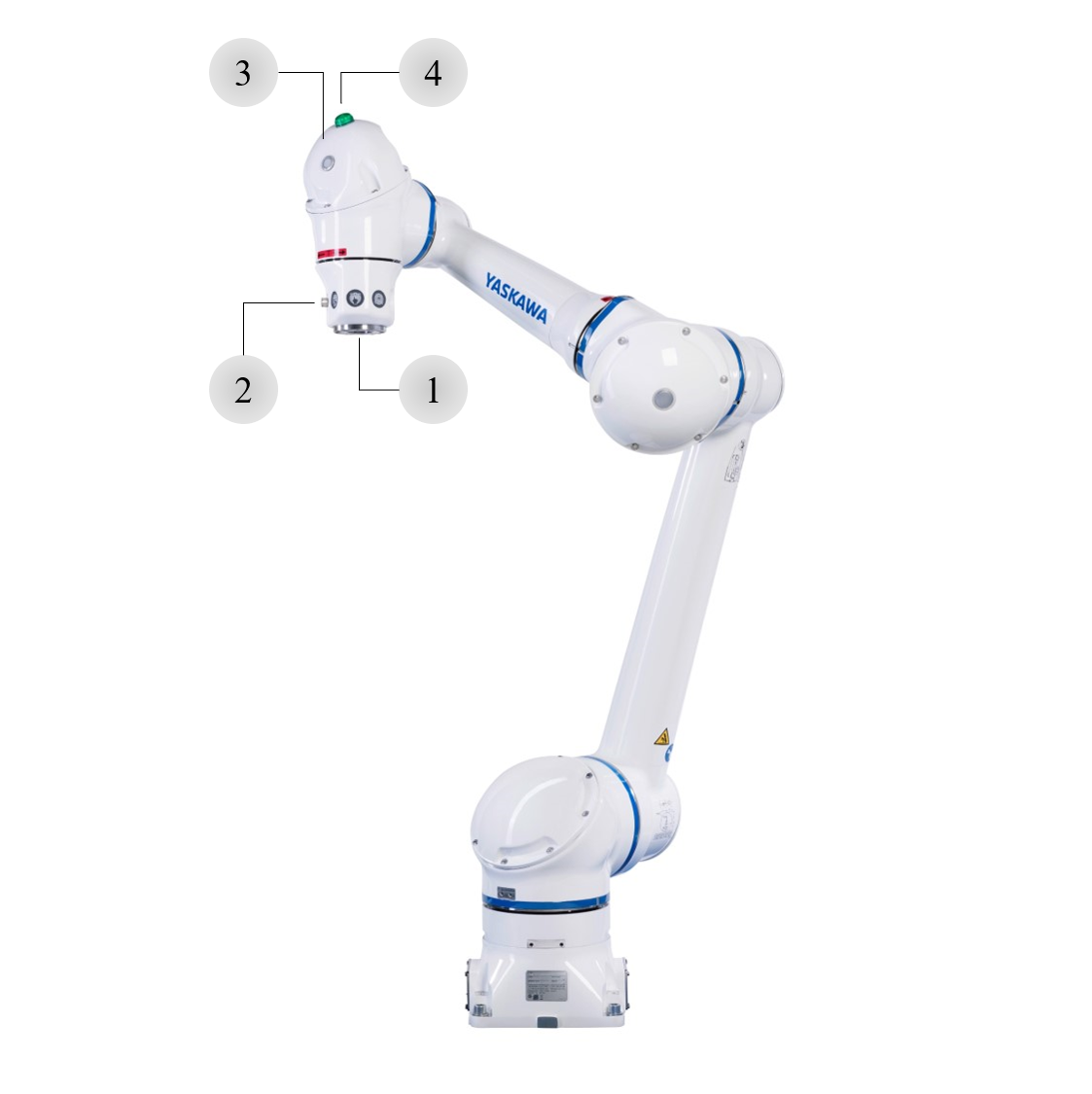
Collaborative Palletizing
Collaborative Welding
Welcome to your first cobot application! In this tutorial you will learn how to build up and program a simple handling robot job. As example, we want to teach our HC cobot how to automatically make a coffee!
Watch the video to understand the process flow!
Your collaborative robot system consists of:
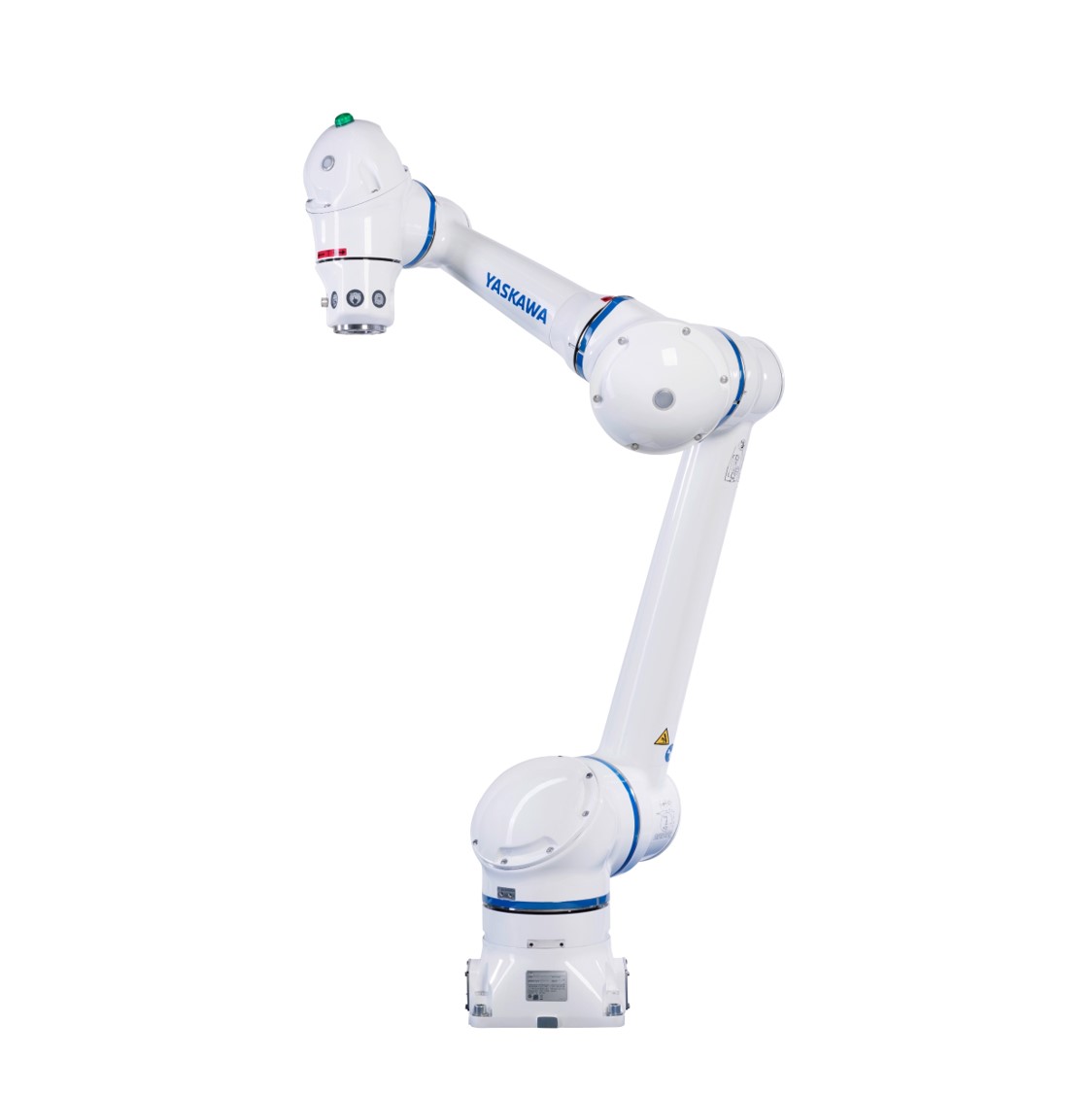
Motoman Cobot HC Series
The MOTOMAN HC10 robot can operate without additional protective measures like a safety fence, depending on the risk assessment. Installation, Setup and Programming is very easy and intuitive, by using hand guiding or Smart Pendant.
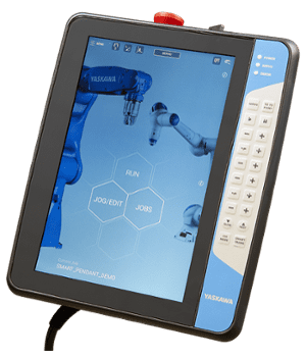
Smart Pendant Operating Device
Our latest pendant does not compromise between
ease of use and capability. The 10-inch touchscreen is
operated like a smartphone with features such as a blend in sidebar, large intuitive buttons or split screen mode Seamless direct teaching integration makes programming with collaborative robots particularly user-friendly.
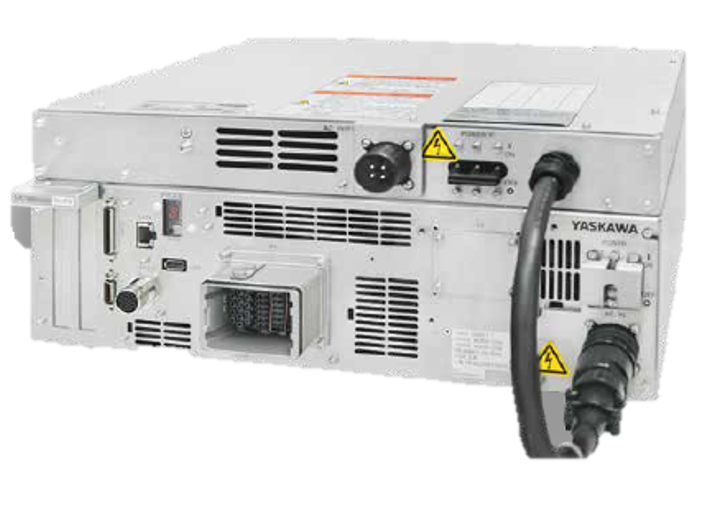
YRC1000 micro controller
Powerful and precise, the compact YRC1000micro controller minimizes installation space whilst optimizing performance. Its small footprint and lightweight are ideal for installations with high-density layouts, where stacking of controllers may be required.
Learn in the following video, how easy it is to setup an HC cobot!
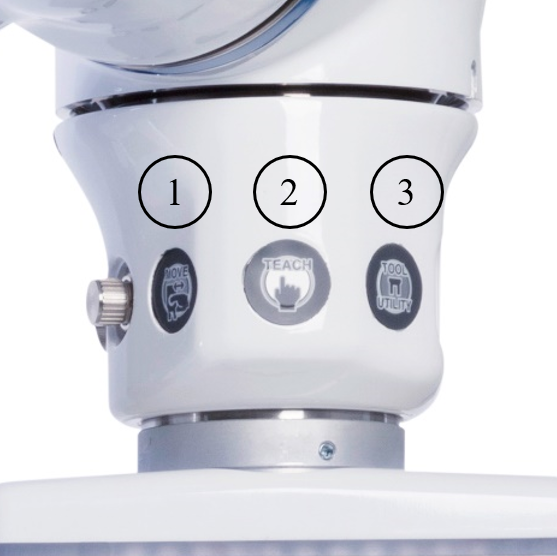
This intuitive programming method is the perfect entry into programming. Simply move the robot flange by hand, record the motion points and operate the gripper actuation by pressing the respective DT buttons. Code is automatically generated in the background on your pendant.
Direct Teach (DT) Buttons:
- 1 MOVE: allows manual robot guiding directly on the robot flange
- 2 TEACH: teach-in positions and generate a respective code automatically
- 3 TOOL UTILITY: Operate tool, e.g. open or close gripper
Learn in the following video, how to guide the robot by hand and teach-in positions!
1) Touchscreen with splitscreen function
2) Emergency Stop
3) Key Switch
4) Membrane Keys
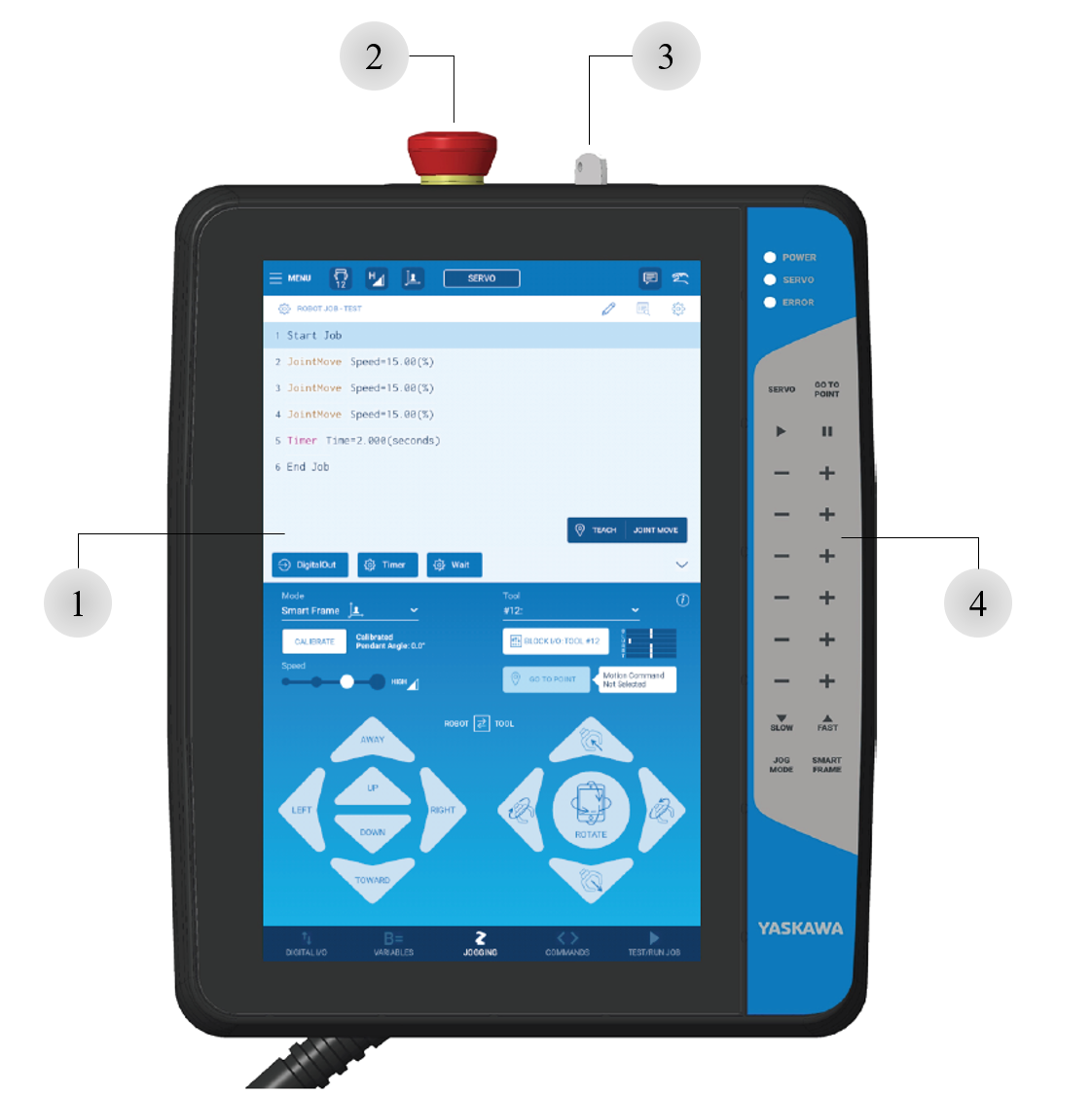
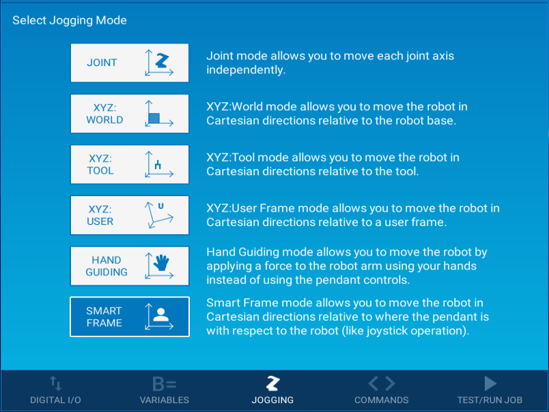
Coordinate Systems
Our patented technology determines the user‘s orientation relative to the robot, supplementing existing
three dimensional coordinate system. This intuitive jogging method works by tilting the smart pendant in
the desired programming direction. Additionally, classic coordinate systems (e.g. world, joint, tool, user frames) are available.
Discover the different coordinate systems in the following video!
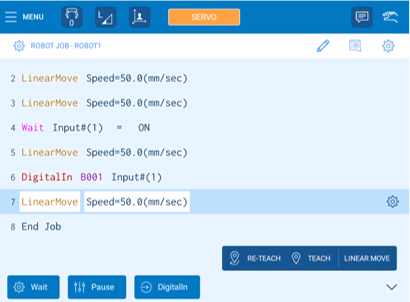
Descriptive Commands:
- Clear text, no abbreviations to memorize
- Easy to review, name & modify
- Various editing possibilities with predefined favourite bar
Learn how to easily program a pick & place job!
Safety Feature Overview
The MOTOMAN HC series with PLd Cat. 3 certificate utilizes 25 safety functions to keep your operator safe. Particular attention was paid to the sensor technology in each joint for increased sensitivity.
PL d Cat. 3 Certificate
25 safety functions
Retract & Clamp Release Function
Pushback Function
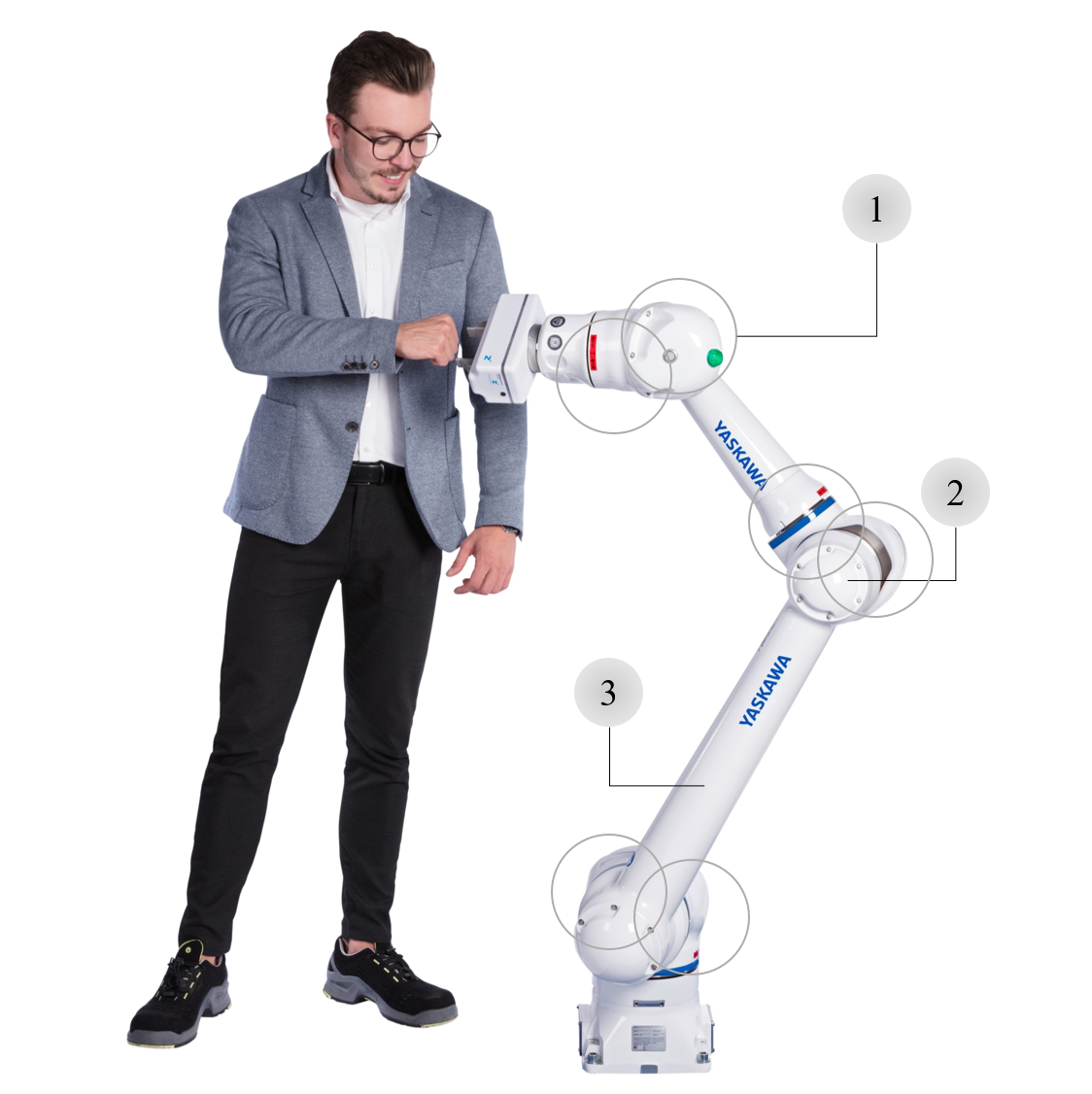
1) Torque sensors in each joint
2) Rounded Edges without Pinching Points
3) Internal Media Routing
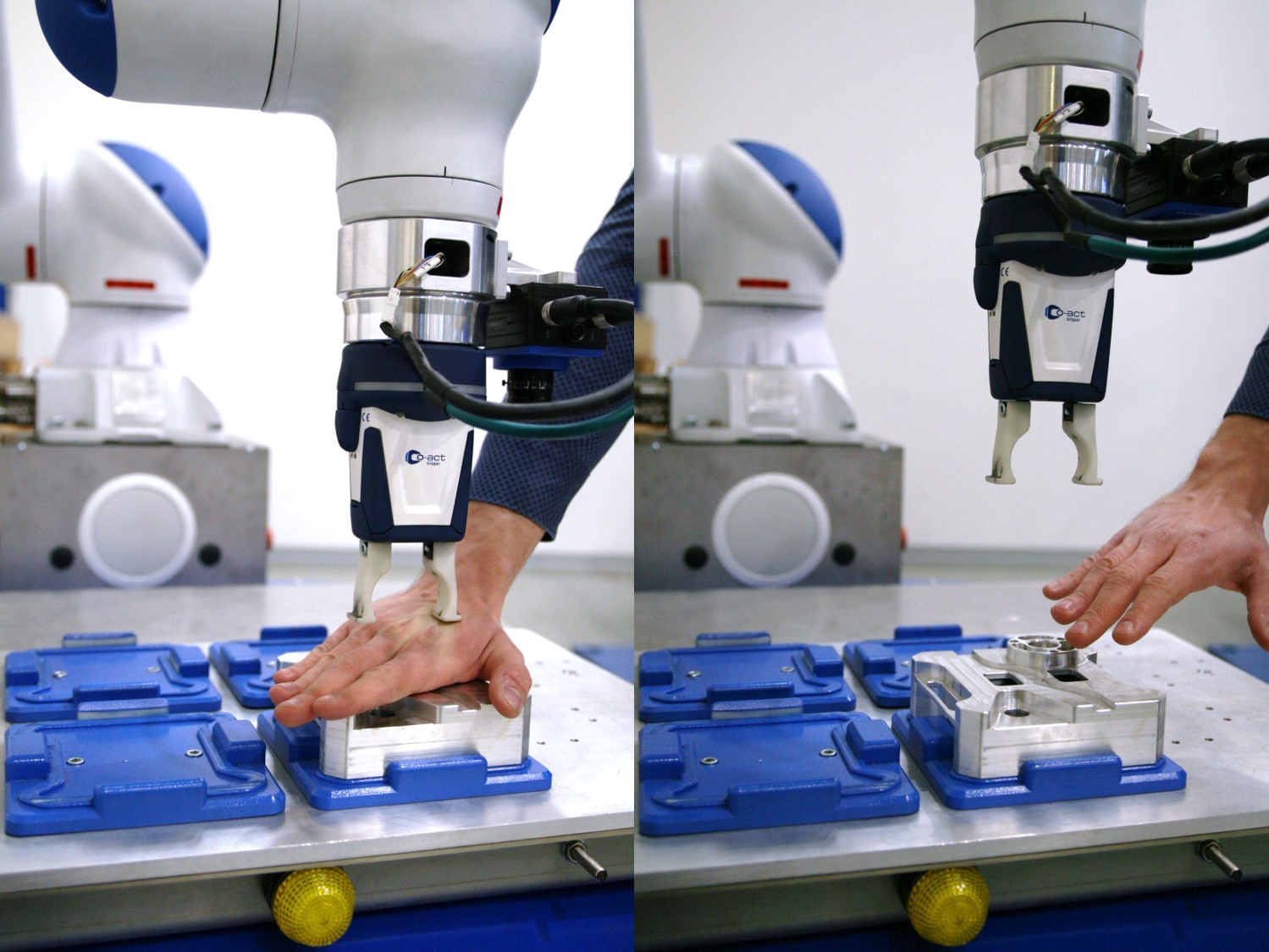
Retract & Anti-Clamp Function
Our unique safety technology helps detect clamping
situations and can react before injury. An immediate robot retract reaction reduces the applied pressure, while the following free drive motion enables the operator to free himself.
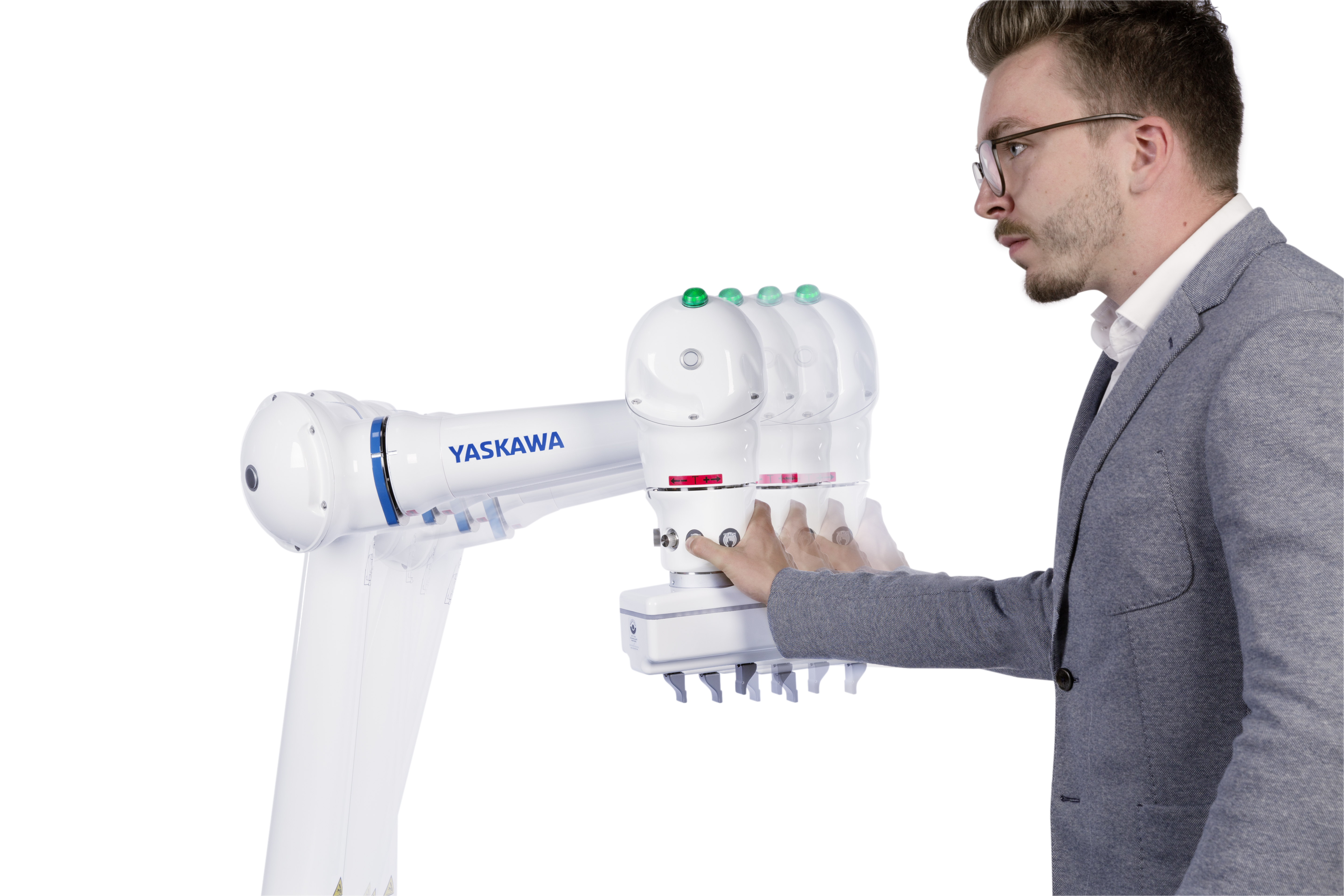
Pushback Function
The robot can be pushed away smoothly whilst in motion, i.e. if the robot is in the way of the operator during manual process. After push back, the robot moves back to it‘s last position and continues his work.
Collision Detection
Each joint is monitored by a single sensor system, that can sense its environment. When a collision occurs,
the HC executes a safe stop. The robot‘s sensitivity is adjustable to adapt to the respective production environment. From sensitive measurement tasks to heavy workpiece handling: the HC robot acts accordingly. This function and the respective collaborative operating speed must be set individually for each application.
Discover how the cobot reacts in case of a collision!
Safety Controller: Functional Safety Unit (FSU)
The powerful Functional Safety Unit monitors the robot‘s movements and sensors and is the control centre of your safety settings. With the simple interface, speed levels and 3D safety areas are quickly defined.
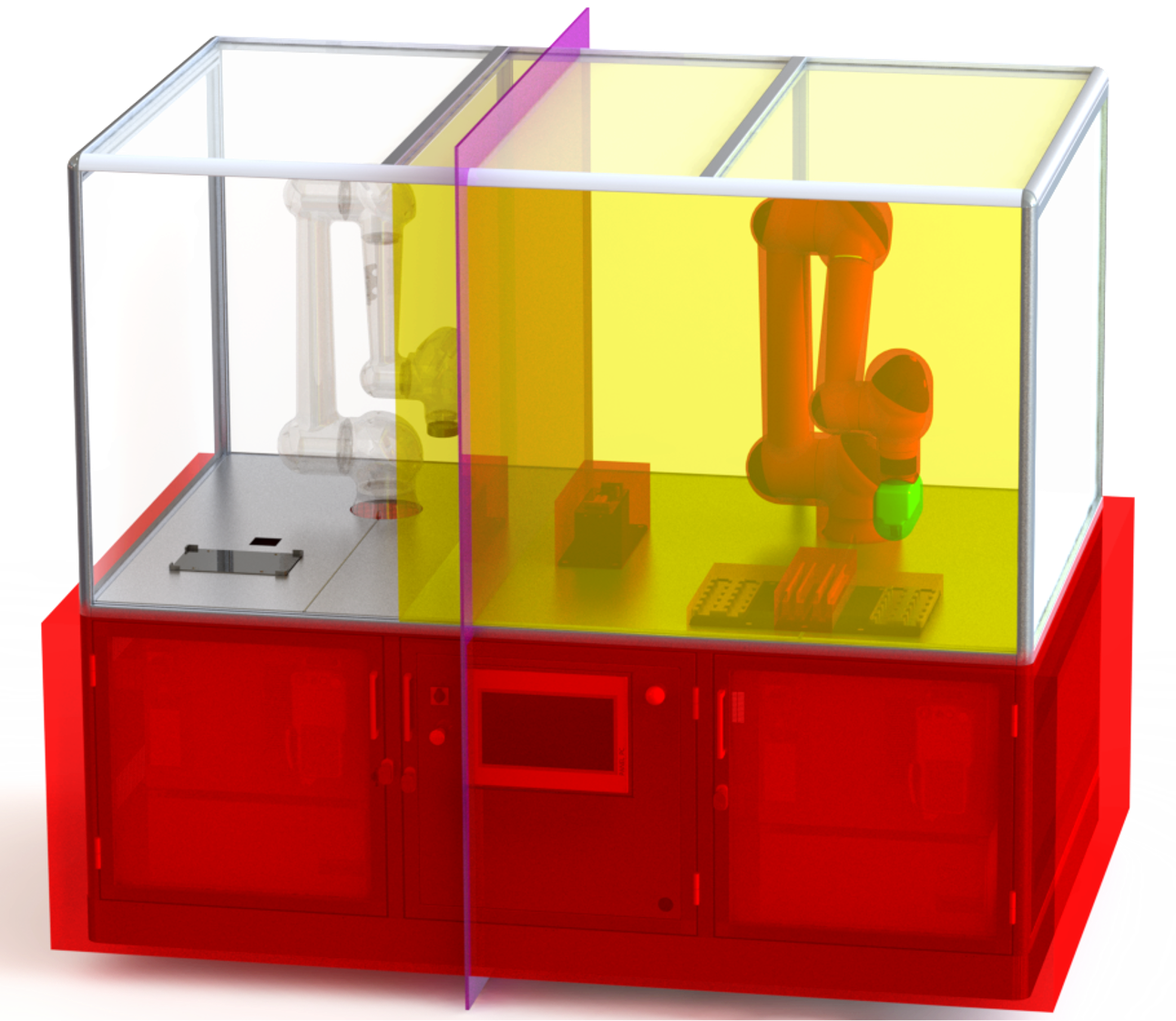
3D Area and Plane Definition
Create safe working areas and individual speed levels:
• Yellow areas to limit the robot’s movement area
• Orange areas to reduce the robot operating speed
• Red areas to ensure collision-free operation
• Planes to lock robots to each other
High-precision Envelope Curves
The robot and tool envelope can be designed very exactly using multiple geometrical elements. This enlarges the available operating space of the robot and increases the safety of the whole application.
Learn how to configurate a 3D safety cube!